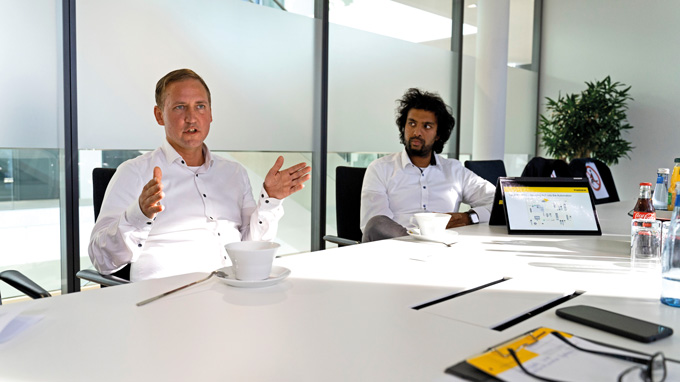
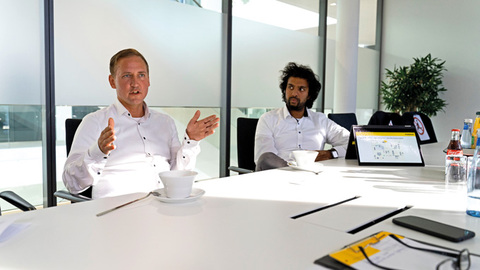
Aurel Buda and Sai Seidel-Sridhavan are convinced that SPE will find its place as a complement to the technologies available today
IO-Link Unlimited
As a specialist in smart sensor technology, Turck brings intelligence to the machine, thus creating the link to Industry 4.0 and IIoT. In an interview with Andreas Gees from the trade magazine elektroAutomation, Turck’s Product Marketing Manager Sai Seidel-Sridhavan and Aurel Buda, Director Product Management Factory Automation Systems, discuss the role of IO-Link as the basic technology in the portfolio and what further developments can be expected in this technology
IO-Link has gained in importance particularly with regard to the concepts for the IIoT. What role does this communication technology have for Turck?
Seidel-Sridhavan: As a founding member of the IO-Link community, we have always worked with our customers to achieve the goal of digital communication from the control level to the last meter in the machine. At that time, we invested in a technology whose development we could not initially foresee. Today IO-Link is an important part of our corporate strategy. Every sensor and communication product we develop for factory automation is available in at least one IO-Link version. Choosing IO-Link is often a strategic decision and IO-Link devices are released first. Besides its use for RFID, IO-Link is one of our two core technologies for digital data from the machine and its use in automation. IO-Link is first and foremost an interface between sensor and controller, but it also provides the basis for implementing IIoT concepts.
Buda: Turck not only produces many different types of sensors for control tasks or process monitoring, but also many more for extensive IIoT solutions. Our customers will ultimately find the complete IO-Link portfolio at Turck, from sensors to RFID read/write devices, power supply units and lights, right through to hubs and masters for I/O systems and block modules – virtually from the sensor to the cloud. All this is complemented by the offering of smart software that makes it much easier for users to deploy the technology. We see IO-Link as the interface between the control and IIoT worlds and so we are also intensively involved in condition monitoring.
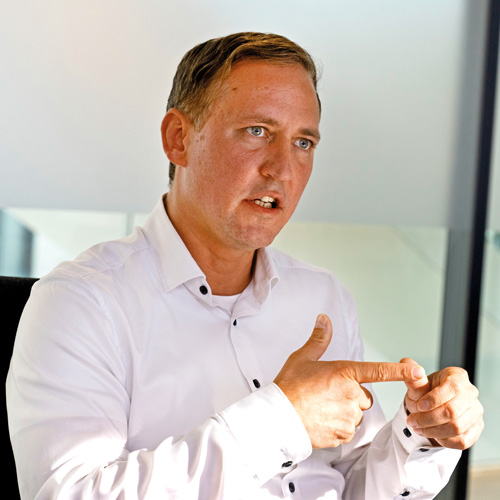
IO-Link initially had acceptance problems. This has changed. Why has Turck developed such an extensive portfolio of devices with IO-Link?
Buda: The efficient networking of even a simple switch in a machine and thus bidirectional communication to the field level is a significant use case at Turck. IO-Link is open and fieldbus-independent. We also support this with our Ethernet multiprotocol strategy in the masters. Sensors range from simple proximity switches to complex devices that provide additional information about their operating status as well as environmental conditions. Our radar sensors, for example, support condition monitoring with integrated analyses of humidity, vibration, temperature, etc. With IO-Link, Turck operates in an ecosystem in which standardized actuator solutions from other manufacturers are also available. That is why we have got prepared for actuator technology on the IO device side. We connect IOs to the master via IO-Link to collect simple sensor signals, but also to switch valves with higher currents.
Seidel-Sridhavan: Acceptance has grown with the increasing availability of IO-Link-capable actuators and many device manufacturers have discovered this interface for themselves. Initially, condition monitoring and IIoT generated interest, but the ecosystem was not complete. Today we are talking about a broad ranging ecology of sensors, valve terminals or power supply units. It has become clear that IO-Link is not only relevant for sensors, I/Os and controllers. Manufacturers are spared the need to integrate different interfaces. Users benefit from this single interface, with identical cables, connectors and software.
IO-Link gained acceptance when the first concepts for IIoT appeared. In the past, users used IO-Link to configure sensors.
Buda: IIoT, condition monitoring, predictive maintenance, process optimization and asset management have boosted the acceptance of IO-Link. Our message has always been that IO-Link also allows a cost-effective infrastructure. IO-Link communicates via an inexpensive standard cable. Although valve terminals or hubs can also be networked using Industrial Ethernet, the costs are significantly higher in this case, whereas the costs of a sensor have not increased due to the integration of IO-Link. And the transfer of process, identification and access data ultimately forms the basis for digital twins and asset management.
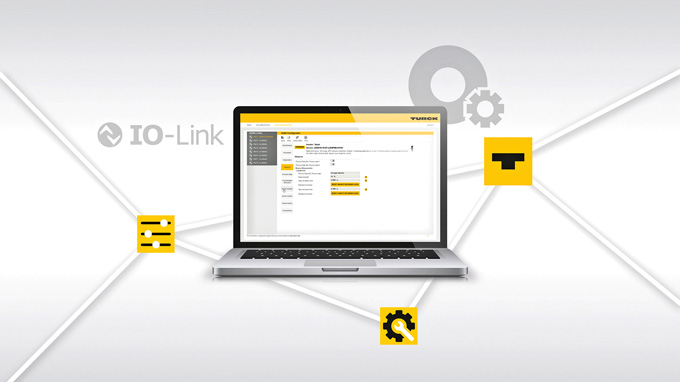
Turck offers solutions from the sensor to the cloud. Which IO-Link software variants are used to support configuration and operation?
Seidel-Sridhavan: Today, we implement the IO-Link configuration directly in Profinet controllers by integrating the data of the IO-Link configuration in the Profinet GSDML file of the master. This means that users can also configure their components in the same engineering system they use for the controller world. We have also integrated a tool into the web servers of our components that allows access to the IODD Finder, a global database of almost all IO-Link devices on the market. The IO-Link device description is then available in the engineering system or in a configuration system via automated interfaces.
Buda: Our web-based configuration tool has the same interface to automatically load the IODDs from the network. The tool is suitable for configuration, but also for initial commissioning. This also applies, for example, to the RFID read/write devices, for which configuration via IO-Link is very simple. We can also, for example, program web apps that facilitate the calibration of sensors. We have implemented this for our radar sensors, but also for our vibration sensors, and we are continuously expanding the range. IO-Link profiles also define the standardized behavior of individual devices or classes. There are already some profiles for RFID devices. This means that devices of the same type can be treated in the same way in terms of software, irrespective of the manufacturer.
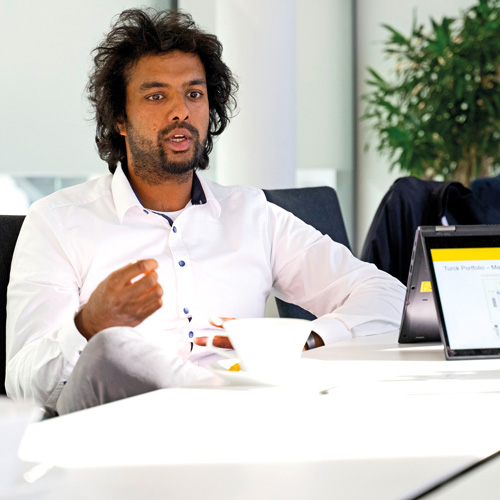
What is the significance of IO-Link for business models such as condition monitoring and predictive maintenance?
Seidel-Sridhavan: The classic automation structure provides for a connection to a PLC. The data goes for example from there to MES systems. Different customer groups, however, are increasingly demanding parallel access directly to the data from the IO-Link masters. This enables the condition monitoring system to thus be expanded or modified as required over the lifetime of a plant. We have been offering this kind of parallel interface in our masters for many years. It enables condition monitoring to be implemented using our edge gateways as well as suitable cloud services. Our concept of decentralized automation not only includes the components outside the control cabinet in IP67, but also the data pre-processing directly at the machine. We also offer logic functions for our edge controller for this purpose. We are also open for industry standards such as OPC UA and MQTT for communication with the IT layer.
Buda: When the topics IIoT and Industry 4.0 emerged, there was a lot of talk about big data to later start machine learning projects. However, a lot of data generates a lot of traffic and requires a lot of bandwidth and memory. Nowadays, only smart data is normally transmitted. This can be an evaluation of the data or its changes, it can also be a data aggregation or the evaluation of correlations between different sensor values. There is also the aspect of latency. Fast response times are ensured when decisions are made directly on decentralized edge controllers.
Is IO-Link therefore ideal as a basis for digital services?
Buda: Our edge controllers provide the platform to preprocess the data using logic or to visualize or send it to the cloud via protocols such as OPC UA. We offer ready-to-use function blocks and modules for this purpose. Our global application engineers and sales teams discuss the task with the customer and draw up a proof of concept. This often goes as far as visualization. However, it often also includes docking to MES or cloud systems. We also work with system integrators who program turnkey applications. Our devices can communicate with any system, but we also offer our own cloud in line with the motto ‘configuring not programming’. The target group is those machine builders who are not so familiar with the world of digital services. They start with remote access and can visualize, store and analyze all data using our cloud service. The end result is turnkey solutions that can be adapted.

IO-Link+ or IO-Link over Single Pair Ethernet is currently a hot topic. How do you assess the latest developments?
Buda: The origins of Single Pair Ethernet come from the automotive industry to replace the CAN bus. SPE has spawned various standards that define transmission lengths and data rates that are also suitable for use in automation and the process industry. In the IO-Link community, we have also taken a close look at the developments and have specified the technology with 10 Mbit over longer distances as IO-Link+. Although this is a different transmission medium, we want to retain the advantages of IO-Link. We do not want to compete with Profinet, Ethernet IP or other Ethernet protocols. IO-Link+ is rather intended for device classes that we cannot serve today. IO Link is limited to 20 m between master and device. The data rate is also less than 1 Mbit. With the advent of IIoT concepts, increased data flows will often be required. Furthermore, IO-Link cannot be used in process automation today. IO-Link+ lays here the foundation for also being able to transmit data up to zones 0 and 1. However, IO-Link will always remain a point-to-point connection.
SPE and protocols such as Profinet could well become an alternative to IO-Link. What are the differences, where are the limits, and what role does cost play?
Buda: One of the expectations of SPE is that it should enable sensor connections at a comparable cost to IO-Link. However, this is very unlikely according to current estimates. It will also hardly be possible to connect sensors over long distances and unshielded cables. In the Profinet community, the unshielded two-wire cables in particular are regarded as a cost benefit. SPE is therefore unlikely to provide such robust communication as IO-Link. There is also a difference on the device side. There are complex sensors where the communication interface does not account for a significant portion of the total cost. SPE should come into play more quickly here. For a simple sensor, IO-Link will assert itself as a fieldbus-independent solution.
An IO-Link master today has four or eight IO-Link ports and therefore connects up to eight devices to the controller via a single connection. On the other hand, if I connect eight sensors via SPE, I have to manage eight individual control connections. This takes up bandwidth, also because of the required protocol overhead. Since each communication link must be set up and managed in the controller, this also requires resources in terms of memory and computing power.
SPE will not be a replacement but an addition to IO-Link. It therefore comes down to a coexistence of alternatives. This also applies to today’s widely used Profinet field devices and other Ethernet protocols. We are convinced that SPE will find its place as an addition to the technologies currently available today.
Seidel-Sridhavan: IO-Link as a technology offers considerable potential for opening up new business areas as well, but performance is limited. Devices requiring a higher data rate are not the focus of IO-Link. We are therefore looking very closely in the IO-Link community at where we can use this technology in a useful way, so that the fluid sensor that yesterday still delivered perfect data with IO-Link is not suddenly only developed with IO-Link+ tomorrow. The community is pushing for coexistence in this respect too. The message is clear, IO-Link+ is an extension not the successor of IO-Link.
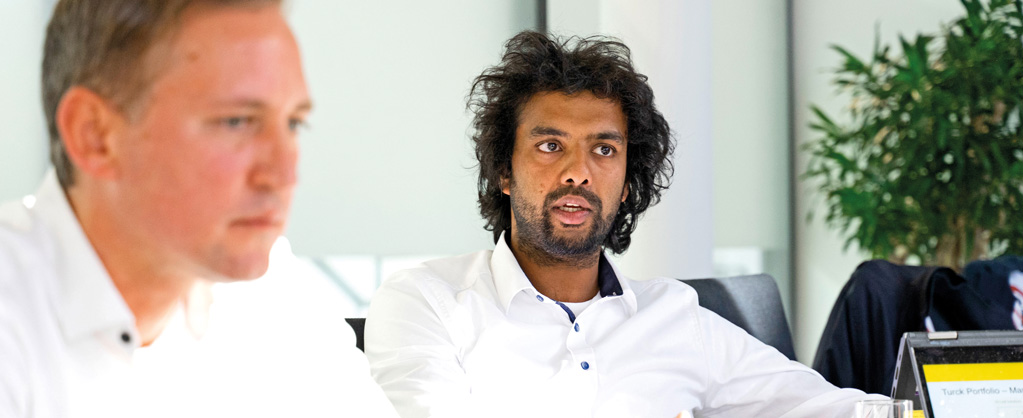
Another topic is IO-Link Safety. What importance does Turck as a safety supplier attach to this technology?
Buda: We are watching the market very closely. Turck offers various safety products, especially in the IP67 area - Profisafe and hybrid devices that combine safety channels and IO-Link, with an integrated shutdown function that can be used to safely switch off actuators. However, this does not comply with the IO-Link safety protocol. The technology as such is interesting and will further advance IO-Link. We are currently watching how the ecosystem is forming up. The first version of the IO-Link Safety standard was already completed in 2017. Alternative approaches such as Profisafe over IO-Link have tended to create uncertainty. After the specification was ready, test concepts were developed as a basis for developing the device. We also consider IO-Link Safety to be an interesting approach because the safety sector in particular is characterized by proprietary sensor and actuator systems. IO-Link Safety is the first harmonized standard at the lower level. This will give us a mixed field of different manufacturers for safety switches and sensors, which can also be connected to masters from different manufacturers.
Seidel-Sridhavan: In recent years, most manufacturers have developed devices for the safety area that link IO-Link with Profisafe. Since these are two concepts, the IO-Link community did not support this. IO-Link Safety, on the other hand, is independent of Profinet, Ethercat or Ethernet IP. Specifications have already been drawn up at the PNO on how IO-Link safety can be integrated into Profinet, and the other organizations are sure to follow. It is important that manufacturers of safety sensors and actuators focus on one standard. A door interlock, for example, has so far required a great deal of effort in terms of wiring. IO-Link Safety with its bidirectional communication would bring considerable advantages here.
Author | The interview was conducted by Andreas Gees, editor of the trade journal elektroAutomation
Select Country
Turck worldwide